Пандемия запустила важный процесс изменения подходов к бизнесу. Появился цифровой взгляд, пришло осознание, что можно уйти от контактных методов работы в онлайн.
Во многих компаниях поняли необходимость уметь быстро перестраиваться на выпуск товаров, наиболее востребованных именно сейчас. Для быстрой перенастройки производственных линий — например, как в случае со средствами индивидуальной защиты и другой медицинской продукцией во время пандемии — необходимо использование цифровых технологий. В новых условиях в компаниях стали особенно востребованы принципы «Индустрии 4.0».
Речь идет о методологии, для которой характерны: обработка больших объемов данных в режиме реального времени; единое информационное пространство для обработки таких данных; использование данных внедрения улучшений в цепочке создания стоимости продукта.
«Индустрия 4.0» позволяет быстро реагировать на изменения на рынке. Например, в условиях пандемии компания Vinfast, с которой мы сотрудничали в автомобильной промышленности, используя методы цифровой подготовки производства и аддитивные технологии, за три недели наладила выпуск компрессоров для аппаратов ИВЛ в объеме 55 тыс. штук в месяц. Без методов цифрового производства такой скорости в запуске новой продукции невозможно было бы достичь.
Актуальность принципов «Индустрии 4.0» связана с появлением интернета вещей, больших данных, аддитивных и других прорывных технологий. Например, в Siemens мы используем их для проектирования эффективных газовых горелок для турбин, у которых сложная геометрия из-за необходимости устройства мощной системы охлаждения.
Возможности big data позволяют изменить сервисную модель турбин, просчитав, когда ее нужно вывести из эксплуатации, отправить отдельные агрегаты в ремонт или напечатать необходимые лопатки или горелки на 3D-принтере в непосредственной близости к месту эксплуатации турбины, что снижает затраты на логистику и сокращает сроки ремонтов.
Благодаря цифровым технологиям мы можем создавать математические модели, которые воспроизводят поведение реального физического объекта. Речь о цифровых двойниках, которые применяются на предприятиях со сложными технологическими процессами, — например, в автомобилестроении, авиастроении и космосе. Кстати, идея двойника впервые была использована в рамках программы Apollo, когда на Земле, используя точную копию корабля, находящегося в космосе, эмулировали различные ситуации, происходящие с ним. Внедрение цифровых двойников на предприятиях позволяет получить четыре основных эффекта. Первый — скорость, время. Второй — стоимость. Технологии «Индустрии 4.0» позволяют на любом этапе контролировать стоимость будущего изделия и выбирать варианты с учетом бюджета и ресурсов проекта. Третий — качество. Цифровые технологии помогают с первого раза изготовить продукт, соответствующий всем требованиям, избежав большого количества итераций. Наконец, четверый эффект — гибкость: при создании изделия сразу возникает понимание, как его можно изменять с учетом конъюнктуры рынка и ограничений в ресурсах.
В России также накапливается опыт использования цифровых двойников и принципов «Индустрии 4.0». Авиастроители из «Иркута» при проектировании самолета МС-21 создали с помощью технологий Siemens не только механический макет лайнера «в цифре», но и спроектировали цифровой электронный макет с бортовыми электросетями. В Объединенной двигателестроительной корпорации создают цифровые двойники авиационных двигателей. Завод КамАЗ создал грузовик 54901, предварительно спроектировав макет его конструкции с помощью цифровых технологий Siemens Digital Industries Software и отработав все технологические процессы сборки новой модели на конвейере в электронном виде. Причем на КамАЗе вплотную подошли и к созданию цифровой электронной архитектуры автомобиля, что очень важно в текущих условиях, когда автомобили становятся более насыщенными электронными компонентами.
В «Волгабурмаше» технологии используются для создания цифровых двойников буровых фрез. В условиях пандемии применение цифровых технологий создает дополнительные преимущества, такое как быстрое развертывание рабочей информационной среды в удаленном режиме. Еще один пример — «Нимбус», небольшая частная компания, которая занимается разработками в области малой авиации.
В ходе проекта все работы по настройке и обучению были выполнены специалистами Siemens на высоком уровне за пять дней в частном облаке, несмотря на дистанционный режим взаимодействия. Такую задачу невозможно было бы решить без современных цифровых технологий и принципов «Индустрии 4.0».
Цифровые технологии и опыт их применения будут обсуждаться 15 сентября на онлайн-конференции Realize LIVE Russia 2020. Это форум для промышленных предприятий, как давно использующих традиционные PLM-системы, так и для компаний, которые выходят за рамки традиционной автоматизации и задумываются о цифровизации своего бизнеса в дискретной промышленности или в процессных индустриях. Эксперты Siemens Digital Industries Software, наши заказчики и партнеры расскажут об эффективных инструментах для адаптации авиационной, космической, автомобилестроительной, машиностроительной, приборостроительной, микроэлектронной и нефтехимической промышленности к быстро меняющимся условиям, об аддитивных технологиях и об интернете вещей.
Распространено мнение, что цифровизация доступна только крупным компаниям с большими бюджетами. Это справедливо лишь отчасти. Действительно, в малом и среднем бизнесе основным фактором, влияющим на решение о внедрении софта, является стоимость владения. Но издержки способно снизить использование облачных технологий, и мой пример с компанией «Нимбус» именно из этой области.
Когда приходят на помощь облачные технологии, малому предприятию не нужно тратиться на инфраструктуру и годовые лицензии на рабочие места — достаточно лэптопов и гибкой подписки с возможностью ее увеличения или уменьшения в нужный момент. Так что современные цифровые решения доступны и компаниям с инженерным персоналом численностью не более двух десятков сотрудников.
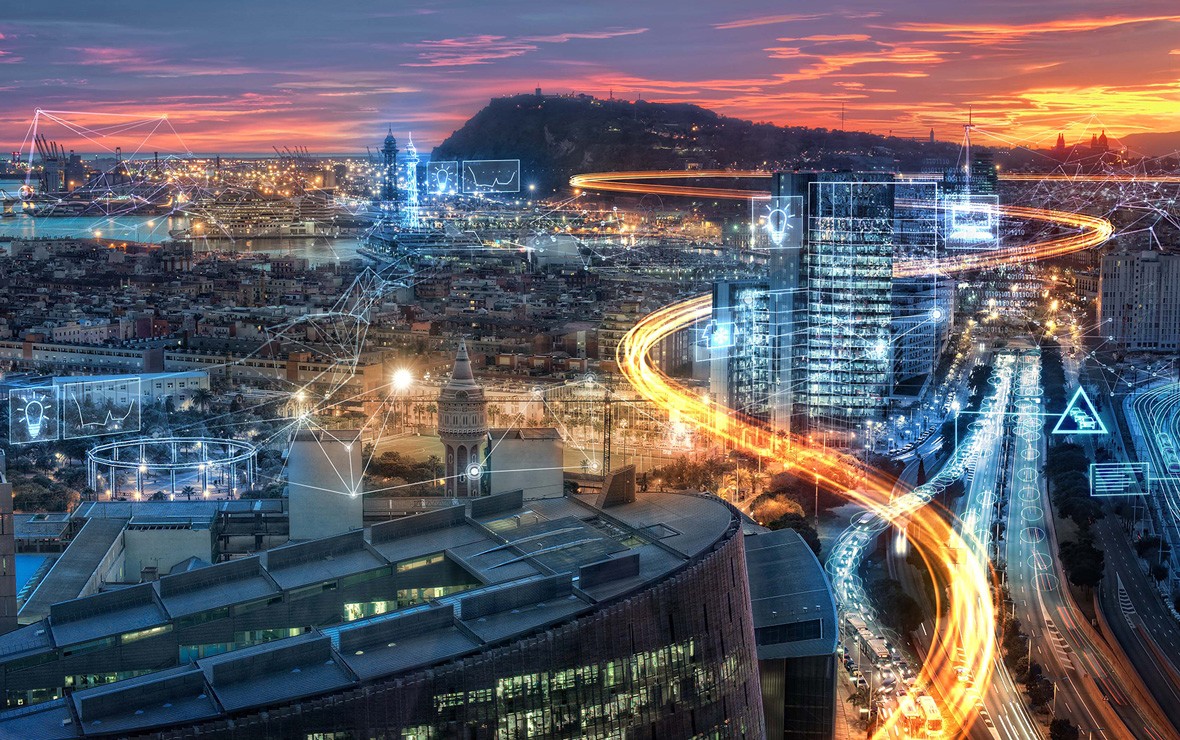
Чем известна Siemens Digital Industries Software
Компания — бизнес-подразделение департамента Digital Factory концерна Siemens, ведущего мирового поставщика программных решений для цифрового преобразования промышленности, обеспечивает новые возможности для воплощения инноваций. Штаб-квартира расположена в г. Плано, штат Техас, число компаний-заказчиков в мире — более 140 тыс.