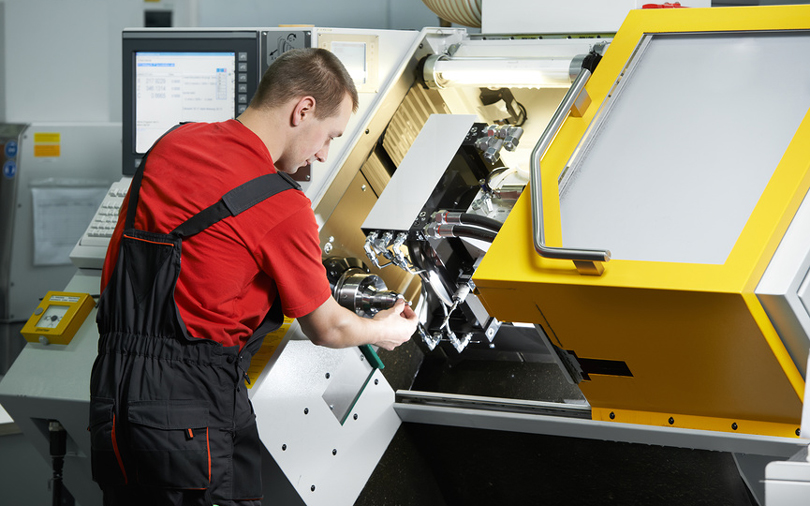
Низкая производительность труда остается одним из главных барьеров для развития российской экономики. Более чем двукратное отставание России в этой сфере от стран Евросоюза, G7 и Организации экономического сотрудничества и развития (ОЭСР) фиксируется российской и зарубежной статистикой. Так, по данным Международной организации труда, в 2005–2015 годах уровень производительности труда в РФ отставал от среднемирового на 27%, от среднего по странам ЕС — на 81%, от среднего по группе G20 — на 41%. В последние годы Росстат зафиксировал дальнейшее падение этого показателя: в 2015 году производительность труда снизилась на 2,2%, а в 2016-м — еще на 0,2%. В 2017 году, по оценке Минэкономразвития, производительность росла вместе со всей экономикой, прибавив за год 1,9%.
При этом российские власти не первый год ставят амбициозные задачи по повышению производительности труда: в «майских» указах 2012 года говорилось о необходимости повысить этот показатель в полтора раза за семь лет, а в последнем Послании Федеральному собранию президент РФ вновь заявил о необходимости повышать производительность в ключевых сферах экономики — промышленности, строительстве и торговле. На этот раз речь шла уже о 5% в год — по словам Владимира Путина, именно такой показатель может обеспечить выход страны на уровень ведущих экономик мира к концу следующего десятилетия. Прогноз Минэкономразвития куда скромнее — при благоприятном сценарии рост к 2020 году составит 2,9%, а в базовом варианте — лишь 1,9%. Еще пессимистичнее настроены в ОЭСР: там полагают, что рост производительности в РФ в 2018–2030 годах не превысит 0,5%.
Наука бережливости
Примеры резкого повышения производительности труда как в масштабах отдельного предприятия, так и целой страны в истории известны. Рост экономики Японии, начавшийся в послевоенные годы, во многом обеспечил курс на повышение производительности в рамках концепции бережливого производства (lean production). В ее основе лежит производственная система Toyota, отцом-основателем которой считается Тайити Оно, прошедший путь от инженера до исполнительного директора компании. Главную задачу он видел в очищении процесса производства от всего, что потребляет ресурсы, но не связано с созданием дополнительной ценности — избыточных запасов, нелогичных транспортировок грузов и перемещений сотрудников, простоев, излишней обработки, переделки дефектов. Оно предложил пятиступенчатый процесс: определить, что представляет ценность для потребителя, выстроить последовательный поток создания этой ценности и обеспечить его непрерывность и «вытягивание» (производство только на основе запроса от заказчика, на каждую стадию производства попадает лишь то, что будет использовано немедленно) и непрерывно стремиться к совершенству, причем этот принцип должен разделять каждый сотрудник компании.
«Все, чем мы занимаемся, — это следим за временем между размещением заказа потребителем и получением денег за выполненную работу. Мы сокращаем этот промежуток времени, устраняя потери, которые не добавляют ценности».
Таити Оно
В отличие от американских автомобильных гигантов вроде Ford и GM, которые стремились сокращать издержки за счет массовости производства, японский производитель, ориентировавшийся на небольшой внутренний рынок, сделал ставку на гибкость. В 1940–1950-е годы Toyota последовательно занималась устранением потерь на всех стадиях производства — от сырья до готового продукта. Достижения компании на этом пути, успешно воспроизведенные и при открытии зарубежных филиалов, привели к популяризации концепции «бережливого производства» во всем мире. На сегодняшний день ее успешно применяют такие компании, как Nike, Amazon, Kimberley-Clark, Caterpillar, Intel и Ford.
Экономить по-российски
В СССР предпринимались попытки совершенствования производственной системы в рамках «научной организации труда», однако в силу нехватки квалифицированных кадров и общих ограничений командной экономики эта работа часто носила формальный характер, а в позднесоветское время и вовсе сошла на нет. В новой России практики «бережливого производства» стали активно внедряться только с 2008 года — флагманами выступили госкомпании РЖД, «Почта России» и Сбербанк.
По словам независимого консультанта в области бережливого производства Валерия Казарина, российский менталитет не мешает внедрению практик, однако национальные особенности все же стоит учитывать, поскольку без добровольного и активного вовлечения сотрудников в процесс результата не достичь. «Нашим людям важно понимать, что и для чего делается, что это означает для них. Можно, конечно, внедрять и директивно, из-под палки, но это будет гораздо менее эффективно», — рассказывает он. Еще одна особенность, ярче всего проявляющаяся на старых предприятиях, — накопленный скепсис. «Люди уже много раз сталкивались с попытками оптимизации, которые начинались и забрасывались, помнят советские разнарядки по НОТ, поэтому они все новое встречают с недоверием», — поясняет Валерий Казарин.
Впрочем, лучшим лекарством от неверия являются достигнутые результаты. По словам эксперта, благодаря бережливым практикам производство в целом может вырасти на десятки процентов, а на отдельных участках можно добиться роста производительности в два-три раза. Так, всего за два года с момента старта программы Сбербанку удалось в четыре раза увеличить объем розничных продаж, сократить очереди на 36%, а перемещения сотрудников в офисе — на 383 км. По словам начальника Центра построения и развития бережливой производственной системы ОАО «РЖД» Сергея Старых, с 2010 по 2017 годы число линейных подразделений компании, применяющих бережливые практики выросло с 47 до 2 тыс, а общее число проектов превысило 5 тыс. В 2013 году это позволило перевозчику сэкономить 560 млн руб, в 2014-м — 1 млрд руб, в 2017-м — 1,14 млрд руб.
Сейчас в списке госкорпораций, делающих ставку на бережливость, — Объединенная вагонная компания» (в 2016 году это обеспечило ей рост производительности труда на основных технологических линиях в среднем на 25% и экономию 195 млн руб.), «Ростех» (технологией уже охвачены КамАЗ, «Вертолеты России», «Авиационное оборудование», концерны КРЭТ и «Калашников», а также Объединенная двигателестроительная корпорация), «Росатом» и многие другие. Среди частных компаний одним из лидеров по внедрению бережливых технологий является группа «Базовый элемент» («Русал», En+, «Русские машины», «Базэл Аэро»).
Трудности масштабирования
Внедрением техник бережливого производства озабочены и на уровне правительства. Так, программа «Бережливая поликлиника», реализуемая корпорацией «Росатом» совместно с Минздравом, уже запущена в 40 регионах. Ее задача — повысить эффективность работы лечебно-профилактических учреждений и общую доступность медицинской помощи, сэкономить время медицинского персонала и пациентов. С 2018 года на ее основе будет создана новая модель первичного звена здравоохранения — по словам главы Минздрава Вероники Скворцовой, в ближайшие три года на нее будут переведены все детские поликлиники России.
Федеральная программа по развитию производительности труда в регионах, подготовленная Минэкономразвития, предписывает предприятиям, претендующим на льготное финансирование, внедрять соответствующие практики. Облегчить эту задачу должны «Рекомендации по применению принципов бережливого производства в различных отраслях промышленности», утвержденные Минпромторгом в июне 2017 года. Их цель — унифицировать lean-методики в различных отраслях и типах организаций. «До последнего времени отечественные предприятия применяли бережливое производство, основываясь на научно-популярных книгах и примерах отдельных успешных проектов, где термины и определения зачастую противоречили друг другу, строгих понятий не было. Стало ясно: промышленникам нужны национальные стандарты», — объяснял необходимость такого документа глава ведомства Денис Мантуров. Кроме того, Минпромторг запустил систему добровольной сертификации систем менеджмента бережливого производства «ЛинСерт»: она гарантирует, что на предприятии должным образом используются механизмы снижения потерь и рисков, а также выступает критерием получения господдержки. С 2018 года модель бережливого производства будет интегрирована и в премию правительства РФ в области качества, а предприятия смогут бесплатно получать рекомендации по его совершенствованию от японских экспертов — об этом недавно сообщил руководитель Роскачества Максим Протасов.
Впрочем, стандартизация методик — вещь неоднозначная, считает Валерий Казарин. «Задачей рекомендаций и ГОСТов было закрепить лучшие практики бережливого производства, однако их не так просто выкристаллизовать», — говорит он. В разработке документов принимало участие множество экспертов, у каждого из которых свой взгляд на бережливое производство, и в результате получилось нечто вроде общего справочника или толкового словаря. Документы не содержат готовых решений, которые рассчитывают найти в них компании. Хотя если не думать своей головой, то никакого бережливого производства все равно не получится», — заключает Валерий Казарин.