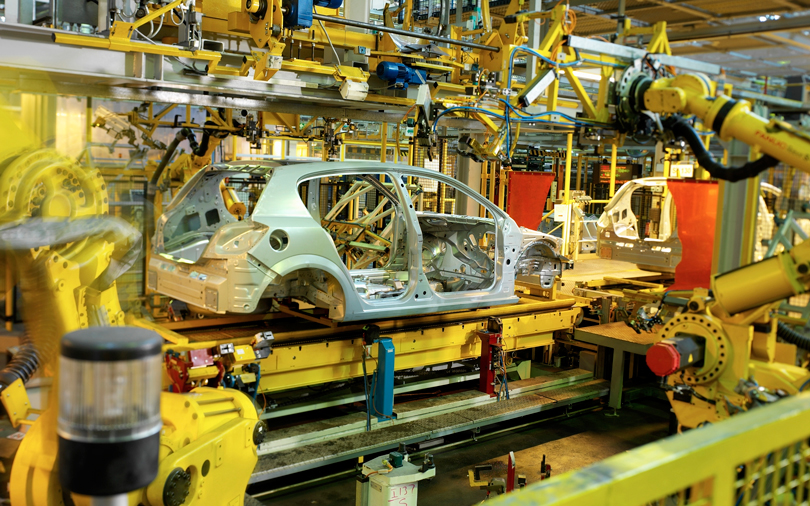
На автомобильных заводах и в конструкторских бюро становится все меньше людей — машины проектируют, сваривают, собирают и окрашивают роботы. Вместо бумажного описания комплектаций на кузова клеят специальный чип, вместо ящиков с запчастями по заводу ездят готовые к установке наборы, автоматически сформированные на складе и доставленные на конвейер беспилотной тележкой. Так сегодня выглядит большинство предприятий автомобилестроения.
Отрасль идет в авангарде цифрового прогресса и является основным потребителем робототехнических решений. Автопром сегодня потребляет более 30% промышленных роботов в мире. К примеру, на заводе Porsche в Лейпциге на выпуске кроссовера Macan задействованы 387 сварочных роботов. В 2017 году 126 тыс. из проданных 387 тыс. промышленных роботов ушло на автомобильные предприятия, по данным Международной федерации робототехники. В России роботов в целом меньше, но и у нас автопром — основной потребитель промышленной робототехники. По подсчетам Национальной ассоциации участников рынка робототехники (НАУРР), около 40% ввозимых в страну роботов предназначены для предприятий этой отрасли. Причем двукратный рост в 2017 году в России закупок робототехники в целом — в прошлом году было установлено более 700 новых роботов — в НАУРР тоже считают прямым следствием выхода из кризиса автомобильной отрасли.
Гибкое производство
В свою очередь, благодаря масштабам потребления автопромом промышленного оборудования сама робототехника сделала большой шаг вперед, утверждает доцент кафедры экономической безопасности РАНХиГС Павел Грибов. Одной из главных причин стремительной роботизации автомобилестроения эксперт считает необходимость обеспечения в отрасли стабильно высокого качества продукции: «Обеспечить ручной контроль каждого автомобиля, когда они выпускается частотой одна машина в несколько минут, невозможно».
По словам вице-президента НАУРР Алисы Конюховской, свою роль сыграла стандартизация производственных процессов и наличие на автозаводах большого числа сложных и вредных для здоровья человека задач, выполнение которых нужно было автоматизировать. Но главное, по ее словам, в том, что «рынок автомобилей высококонкурентен, повышение эффективности производства и снижения издержек критически важно».
Рентабельность в автопроме возможна только за счет быстрой, качественной разработки и сборки и с наименьшими затратами, объясняет завкафедрой робототехнических систем МГТУ имени Баумана Владимир Серебренный. Именно поэтому, уверен он, все передовые технические решения сегодня внедряются не в военных отраслях, как это было раньше, а в автостроении: «Так было с роботами, автоматическими линиями и комплексными производственными системами — все они вначале проходят через автостроение».
Новые технологии производства оказываются особенно актуальными в сегментах, связанных с массовым покупателем, отмечает Владимир Серебренный: «Если бы АвтоВАЗ не стремился внедрять технологии, он давно перестал бы быть конкурентоспособным». Сегодня предприятия АвтоВАЗа являются одними из самых развитых в стране, согласен Павел Грибов: «Конвейер ВАЗа модернизируется под стандарты Renault. Это, возможно, не самые передовые технологии, но экономически очень эффективные».
Концепция автоматизации производства до 2020 года, которую внедрил российский КамАЗ, предполагает установку более 900 робототехнических комплексов механообработки, сварки, литья, окраски, штамповки и сборки. В ходе модернизации на КамАЗе появятся лазерные сварочные комплексы, будут запущены экологически чистые процессы термообработки и окраски, технологии лазерной наплавки и термообработки штампов, а также 3D-принтеры.
От роботизации на КамАЗе ожидают значительного экономического эффекта, 60–70% которого будет достигнуто за счет большей производительности и гибкости производства, 15–20% — за счет уменьшения процента брака, еще 10–15% — благодаря экономии на оплате труда сотрудников. В свою очередь, Павел Грибов утверждает, что основная экономия при роботизации заключается именно в отсутствии брака, то есть затрат на исправление дефектов, а также репутационных потерь компании. Эксперт приводит в пример китайские автомобильные компании, на заводах которых в 1990-е годы было много ручного труда, а понятие качества китайской машины стало нарицательным: «Все поменялось в последние годы именно благодаря внедрению автоматизированных технологий производства. Сегодня можно быть уверенным, что все автомобили в партии будут сделаны по одному стандарту с одним и тем же качеством».
При этом говорить о сиюминутной экономии едва ли возможно, предупреждают эксперты. Павел Грибов утверждает, что внедрение роботов приводит к значительному удорожанию производства: «Если сравнить завод Ford во Всеволожске в начале двухтысячных, когда локализация была невысокой, и завод PSA под Калугой, построенный на 12–15 лет позже, то разница в их стоимости будет значительной. Высокоавтоматизированный завод дороже в разы, зато он позволяет снизить количество дефектов и стандартизировать качество, что в итоге перекроет все затраты».
Помимо сварки и окраски кузовов на автомобильном производстве можно автоматизировать сборочные операции, производство силового агрегата, механосборочную часть. Не менее важной является гибкость всего производства, говорит Владимир Серебренный: «Гибкие производственные системы позволяют быстро переналаживать конвейер, переходить с одного вида продукции на другой и в итоге иметь достаточно высокие экономические показатели». Если раньше при переходе на другой вид продукции заводу приходилось решать целый комплекс вопросов, связанных с конструированием, подготовкой производства, изготовлением оснастки, на что могли уйти годы, то теперь речь может идти о днях или даже минутах.
Цифровой стандарт
Поручить машине дизайн автомобиля конструкторы пока не готовы, а вот расчет технических параметров давно ведется в автоматическом режиме. «В Японии это приводит к сокращению срока разработки и постановки автомобиля на производство. Если в 2000-х годах Ford тратил на цикл подготовки производства новой модели больше двух лет, то сегодня японцы вполне укладываются в 12 месяцев», — говорит Павел Грибов.
Проектирование автомобилей тоже давно ведется на компьютерах. «Renault Logan был первой в истории машиной, разработка которой велась полностью в цифровой среде, от проектирования до проведения виртуальных испытаний», — отмечает Владимир Серебренный. При этом многие детали апробировались на макетах, а готовый автомобиль подвергался реальным краш-тестам, но в целом процесс шел гораздо быстрее. В итоге циклы подготовки и постановки на производство значительно уменьшились, а цифровое проектирование стало отраслевым стандартом.
Еще одна перспективная область автоматизации — внутризаводская логистика и складское хозяйство. Доставка со склада на конвейер, комплектование и даже размещение заказов у поставщиков автоматизируются уже сейчас. Так, московский завод «Renault Россия» с 2016 года развивает собственный проект по внедрению беспилотных перевозок комплектующих внутри завода. Российские роботы-перевозчики умеют вращаться на 360 градусов, поднимают до 1250 кг, могут преодолевать рельеф покрытия и небольшие препятствия, а также следить за другими беспилотниками, чтобы избегать столкновений. Сегодня на заводе используются 110 таких транспортных средств. Такие же тележки «Renault Россия» поставляет на завод АвтоВАЗа в Ижевске.
Кроме того, именно в России была разработана информационная платформа для логистической системы, которая обеспечивает не только работу склада, но и коммуникацию с дилерами, а также автоматизацию заявок для перевозчиков. Эта система, принятая в качестве стандарта для альянса Renault-Nissan-Mitsubishi, внедряется на заводах во всем мире.
А вот 3D-принтеры широкого применения в автопроме пока не нашли. «Массовое производство деталей на таких принтерах пока нецелесообразно, обычное оборудование дешевле и может долго служить», — говорит Павел Грибов. Сегодня 3D-принтеры используются только для создания сопутствующей оснастки. На московском заводе Renault с их помощью «печатают» защитные элементы для используемых инструментов, а выгода от такого производства оценивается в 1 млн руб. в год.
Отказ от конвейера
Конвейер некогда появился именно в автопроме, и сегодня именно эта отрасль задает моду на отказ от конвейерного производства. «Volvo этим вопросом озаботилась еще лет 15 лет назад, сейчас меняется группа Volkswagen, внедряя использование модульных архитектур», — говорит Павел Грибов.
Почти достигнув совершенства в производстве, автобренды начинают менять сам продукт и создавать новые рынки. «Переход с двигателей внутреннего сгорания на электрический двигатель меняет производство в той степени, в которой это нужно для использования других компонентов, но в корне идеологию не меняет. Беспилотники также требуют новых компонентов, но не другого производства», — отмечает Владимир Серебренный.
Рабочие прототипы автономных транспортных средств уже существуют у Audi, BMW и Mercedes-Benz, а из массовых марок наибольших успехов добились Ford, который строит целые города-полигоны для испытаний беспилотников, и Nissan, уже сегодня пробующий самоуправляемые машины на улицах японских городов. В России беспилотниками всерьез занимается КамАЗ, у которого есть несколько совместных проектов с различными ИТ-компаниями.
Автопроизводители инвестируют в разработки беспилотных технологий миллиарды долларов: Ford намерен вложить в разработку беспилотных технологий около $4 млрд до 2023 года, Hyundai — $22 млрд в ближайшие пять лет, General Motors вместе с правительством США обещали инвестировать $26 млрд в создание целого исследовательского центра. Рынок беспилотников через 20 лет, по прогнозу консалтинговой компании A.T. Kearney, достигнет $560 млрд.