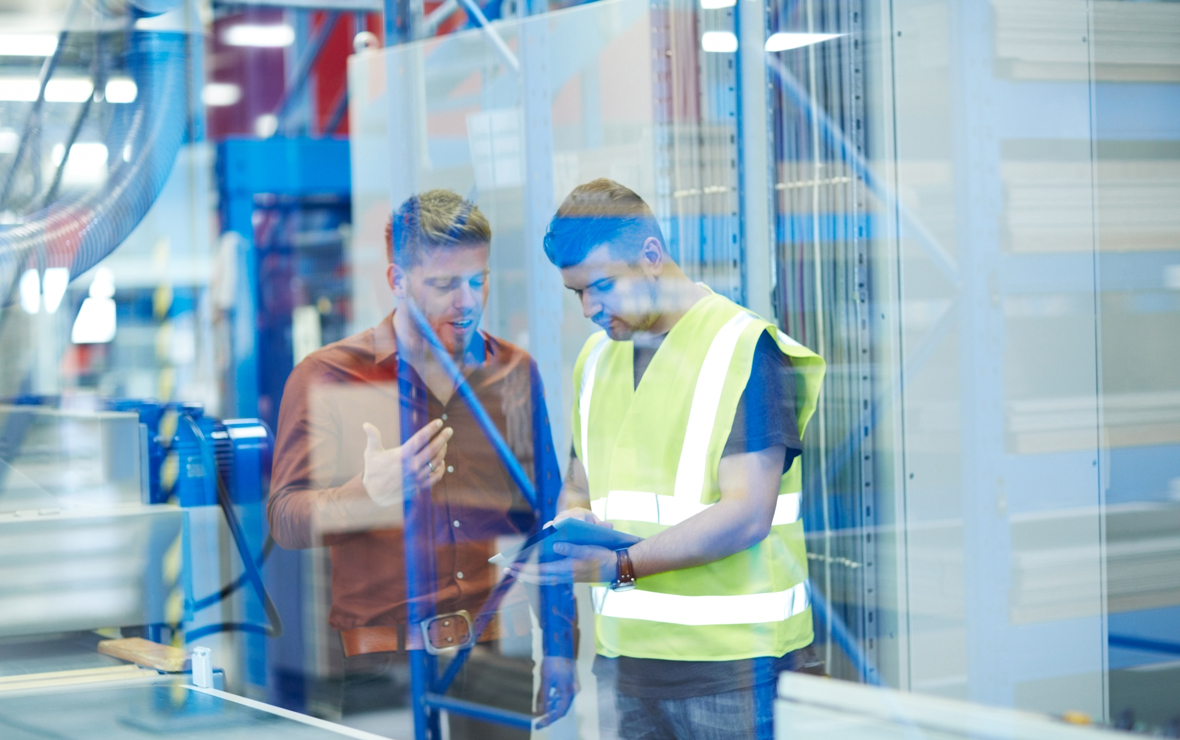
Опыт № 1: пилот для транспортников
АО «Автовазтранс» (Самарская область) присоединилось к нацпроекту «Производительность труда и поддержка занятости» в апреле 2019 года. Компания является одним из крупнейших транспортных предприятий России и оказывает услуги по перевозке грузов автомобильным и железнодорожным транспортом, а также его техническому обслуживанию и ремонту.
Результатом работы Федерального центра компетенций (ФЦК) на предприятии стало увеличение количества технически обслуженных автомобилей «КамАЗ 5490» с шести до 120 на каждого сотрудника в месяц. Рабочая группа, состоявшая из специалистов компании и экспертов ФЦК, выбрала для оптимизации поток, на котором проводится техническое обслуживание (ТО-2) автомобиля «КамАЗ 5490», потому что это самый востребованный в России грузовик, а доля ТО-2 в общем объеме услуг этого участка составляет 24% и приносит 10% выручки предприятия.
Такого результата удалось достичь за счет проведенной экспертами стандартизации операций — время ТО сократилось с 97 до пяти часов на единицу транспорта. Уменьшилось расстояние, которое проходил рабочий в поисках нужного инструмента и расходных материалов (с 1732 до 300 м). Кроме того, на участке-образце было оптимизировано количество персонала. Причем число работников было не уменьшено, а увеличено: здесь стали работать двое сотрудников с эффективной загрузкой каждого 90% (до этого один человек последовательно выполнял все действия по ТО, что требовало много времени для обслуживания автомобиля). После обучения экспертами ФЦК работники компании создали панель управления участком ТО, где проводились ежедневные производственные совещания.
Коммерческий директор компании Александр Поляков говорит, что участие АО «Автовазтранс» в нацпроекте оказалось полезным как для управленцев, так и для рядовых сотрудников. А проектная группа переросла в отдельный офис, в котором появился сертифицированный тренер. За рационализаторство работников стали поощрять: изначально они отнеслись к этому скептически, но быстро оценили плюсы нового подхода. «Взгляд со стороны на наши внутренние процессы оказался крайне важен, и мы запустили еще один проект. Бережливое производство действительно позволяет без существенных финансовых затрат заметно улучшить показатели», — заключает Александр Поляков.
Опыт № 2: ферма без потерь
Инструменты бережливого производства могут быть применены не только на предприятиях, специализирующихся на автокомпонентах или автопроизводстве, а в любых отраслях. Таким примером стало первое сельскохозяйственное предприятие — участник нацпроекта: АО «Белгородские молочные фермы» (Белгородская область), вступившее в нацпроект в январе 2019 года. Компании принадлежат две молочные фермы, где без привязи содержатся почти 5 тыс. коров. Она также занимается откормкой крупного рогатого скота и владеет пахотными землями площадью более 15,5 тыс. га, которые обеспечивают собственную кормовую базу.
В рамках пилотного проекта эксперты модернизировали доильный зал (процесс производства молока в суммарной выручке компании занимает 52%). Одной из основных проблем, выявленных специалистами, стала неравномерная загрузка доярок. Для устранения этих потерь были реорганизованы их рабочие места, проанализированы перемещения, проведен хронометраж дойки и разработан стандарт выполнения операций. В результате обязанность пополнять запасы расходных материалов была передана от операторов доения вспомогательному персоналу, были полностью устранены ненужные перемещения доярок по цеху. Это позволило сократить время дойки одной коровы с 15 минут 45 секунд до 13 минут 33 секунд и ввести дополнительный цикл дойки, в результате чего объем выпуска молока увеличился с 50 до 55 т в сутки.
Замдиректора по повышению эффективности производства компании Ольга Тарасова рассказывает, что услышала о бережливом производстве в ноябре прошлого года и поняла, что старалась следовать подобному подходу всю жизнь. «В него заложен здравый смысл», — поясняет она. По словам Ольги Тарасовой, эксперты ФЦК сразу поставили амбициозные задачи и поначалу производственники компании не верили в то, что они могут быть решены.
«Методологический подход ФЦК выверен — они передают чистую практику», — свидетельствует Ольга Тарасова, отмечая, что в результате на предприятии улучшились условия труда, а у доярок появилось больше времени для отдыха. «Мы стали прислушиваться к людям, ведь никто не может улучшить место работы, кроме человека, который на нем работает», — называет еще один плюс участия в нацпроекте руководитель по повышению эффективности производства АО «Белгородские молочные фермы».
Опыт № 3: подход к снегоходу
Концепция бережливого производства развивалась ФЦК в рыбинском АО «Русская механика» (Ярославская область) в марте — сентябре 2019 года. «Мы занимаемся бережливым производством с 2009 года, достигли определенных успехов, после чего «тема легла», — поясняет мотивацию глава предприятия Леонид Можейко.
Компания специализируется на выпуске автомобилей спецназначения, в ее штате трудятся более 800 сотрудников. Проект было решено запустить на участке производства снегоходов: время изготовления одной из моделей снегохода было нестабильно. Диагностика производства позволила экспертам ФЦК выяснить, что фактическое время изготовления снегохода составляет 157 дней. Среди основных причин этого оказались простои сборщиков конвейера на девяти из десяти рабочих мест. Кроме того, при замещении и перемещении работников не всегда учитывались их навыки, что вовлекало в производственные процессы недостаточно компетентных сотрудников. В качестве решения была разработана матрица компетенций, которая позволила привести навыки работника в соответствие с занимаемым им местом у конвейера и обучить персонал компетенциям, которые требуются на соседних рабочих местах. В результате время выполнения операции снизилось на 25%, а загрузка операторов сборочного конвейера выросла, фактическое время изготовления снегохода снизилось до 80 дней.
Кроме того, было решено вывести из процесса производства некоторые операции. Это в том числе коснулось нарезания трубок и распаковки коробок, которые были выведены за пределы работы конвейера. Операции же по рабочим местам распределили так, чтобы равномерно загрузить операторов. Результат: общий простой сократился с 48 до 13 минут, а скорость движения конвейера выросла. Потери, связанные с излишними перемещениями, устранили, изменив маршруты изготовления комплектующих снегохода, что сократило транспортировку более чем на 280 м.
Экспертам также удалось выяснить, что в нужное время к месту проведения операции иногда не поступают двигатели, отчего простаивали сборщики на конвейере. При выдаче и получении двигателей со склада была внедрена система автоматизированного соблюдения принципа FIFO — получение в порядке очереди.
«Благодаря экспертам ФЦК мы снова обратили внимание на потенциал бережливого производства. Кроме того, участие в нацпроекте позволило нам системно взаимодействовать с его основными субъектами, в том числе Минэкономразвития, что стало дополнительным катализатором внутренних преобразований. Мы получили заметный рывок в эффективности и много активностей стали оценивать с точки зрения бережливого производства», — заключает Леонид Можейко. Усовершенствование производственной системы, утверждает топ-менеджер, позволит компании претендовать на льготный заем от Фонда развития промышленности — до 300 млн руб. под 1% годовых сроком до пяти лет, который можно направить на реализацию проектов по повышению производительности труда.