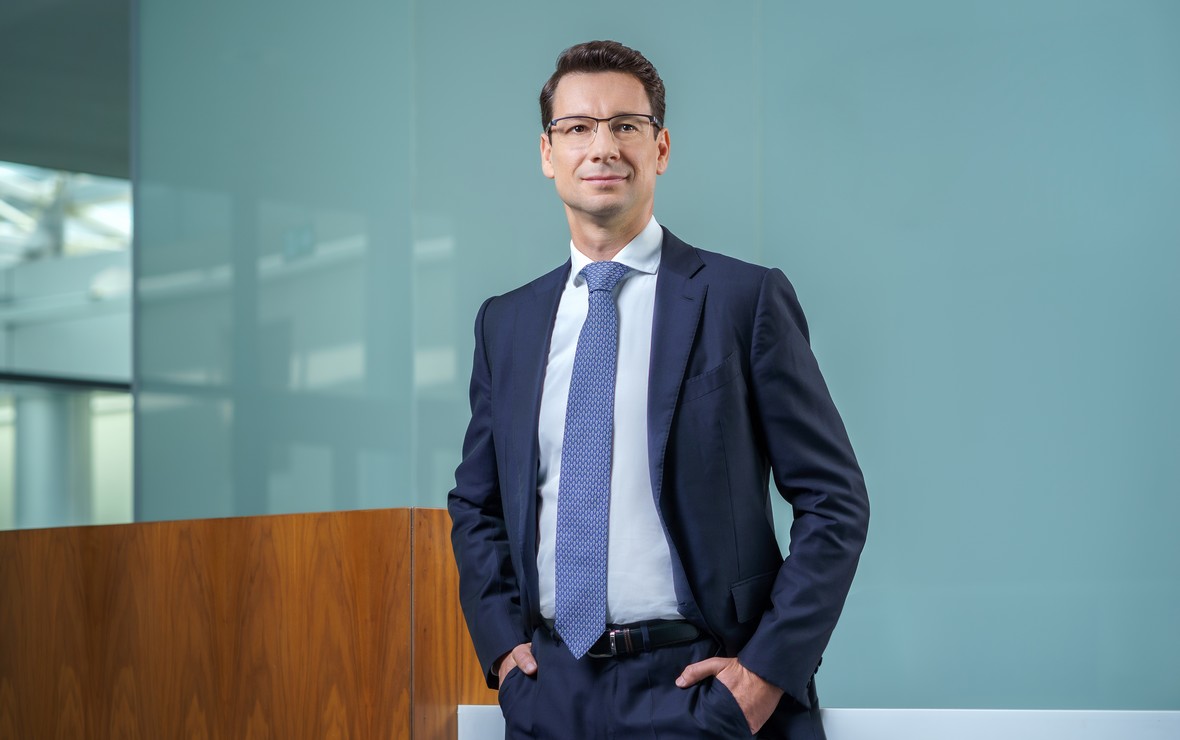
— Как вы оцениваете цифровизацию промышленности в России?
— Степень цифровизации производств в разных отраслях и сегментах рынка серьезно отличается. Цифровые технологии активно используются, например, в машиностроении, металлургии, добыче и транспортировке нефти и газа, химической и нефтехимической отраслях. Причем в России есть компании, не только определившие для себя цифровизацию как стратегию бизнеса, но и уже добившиеся практических результатов, такие как «Газпром нефть», «Сибур», КамАЗ, «Транснефть», «Северсталь», «Русал», ММК.
Среди отраслей, где цифровые инновации пока менее распространены, высокий потенциал у ОЕМ-производителей, предприятий пищевой промышленности и коммунальной инфраструктуры, а также занятых в сфере переработки мусора.
В целом в промышленности идет активное строительство платформ и экосистем, растут число и зрелость цифровых инструментов. Увеличилась потребность в цифровом консалтинге, сквозных цифровых компетенциях и апробированных инструментах высокой степени готовности.
Заметная отдача и пересмотр бизнес-моделей — следующий этап цифровой трансформации. Для этого необходимо развивать инфраструктуру и наращивать критический уровень цифровизации в отраслевом и межотраслевом взаимодействии, что требует в том числе развития нормативного регулирования, а также готовность руководства компаний к изменениям корпоративной культуры и процессов на предприятиях.
— Пандемия повлияла на потребности в цифровизации бизнес-процессов? Спрос на какие решения заметно увеличился?
— Ограничения экономической и социальной жизни показали, что определять дальнейшую работу предприятий будет в том числе возможность выполнять задачи удаленно и в цифровом формате.
Вырос спрос на цифровые услуги и продукты в целом, при этом в приоритете — экономический эффект. С учетом нестабильности рынков и финансовых систем существенно сокращаются сроки реализации проектов. Это усиливает потребность в готовых комплексных решениях. Заказчики хотят использовать готовые инструменты с подтвержденной эффективностью, внимательно смотрят на имеющиеся кейсы и отраслевой опыт, прорабатывают все более комплексные задачи и сценарии использования.
Объединение «Атоммаш», например, внедрило вибропаспорта и технологии предсказательной диагностики станков для предупреждения сбоев. «Транснефть» полностью перестроила систему диспетчерского контроля и управления. «Сибур» реализовал систему обнаружения утечек на трубопроводах на основе технологий анализа данных и с использованием дронов. Это обеспечит бизнесу возможность перехода к новым моделям обслуживания инфраструктуры. Компания также активно внедряет цифровые двойники. Завод «Станкомашкомплекс» расширил на основе цифровых двойников и технологий промышленного интернета вещей цифровые сервисы для своей станочной продукции. Это лишь некоторые из ярких примеров.
Современное производство генерирует огромный объем данных; чтобы на их основе принимать решения, необходимы мощные системы. Открытая облачная платформа MindSphere «Сименс», например, обеспечивает связь физической инфраструктуры с цифровой средой, дает возможность эффективно использовать оборудование на основе анализа данных.
Кроме того, возникли новые требования к сервису. На пике пандемии его проведение усложнилось, поскольку физическое присутствие рабочих на объектах не всегда было возможным. Поэтому промышленность ждет современных решений, не требующих или почти не требующих сервисного обслуживания.
Дополнительными стимулирующими факторами для цифровой трансформации и автоматизации процессов в промышленности стали географическая удаленность объектов в России и дефицит необходимых компетенций в отдельных регионах. Цифровизация позволяет организовать централизованный удаленный доступ, помогая решить эти вопросы.
— Локализация производства оправдала себя в условиях пандемии? Как продвигаются ваши проекты?
— В стратегии локализации мы всегда делали ставку на развитие не только производств, но и локальных компетенций по всей цепочке создания добавленной стоимости в России: НИОКР, производство, проектный менеджмент, сервисное обслуживание. В частности, локализация сервиса помогла нам в период пандемии — мы своевременно оказывали сервисную поддержку силами российских специалистов.
Мы продолжаем развивать все наши локальные площадки. В прошлом году мы, например, отметили десятилетие производства высоковольтного оборудования в Дубне. Особое внимание мы уделяем развитию железнодорожного кластера — нашему совместному с группой «Синара» предприятию «Уральские локомотивы» и сервисным депо.
— Какие цифровые решения вы развиваете в рамках железнодорожного кластера?
— «Сименс» создала железнодорожную версию масштабной облачной платформы Siemens MindSphere — систему Railigent, которая связывает оборудование и физическую инфраструктуру с цифровым миром. Система позволяет работать с данными от подвижного состава и объектов железнодорожной инфраструктуры и включает «умный» мониторинг, аналитику, в том числе глубокий анализ причин выхода из строя разных элементов, а также предиктивную аналитику отказов.
В рамках сотрудничества с компанией «Уралхим-Транс» мы разработали цифровой сервис по мониторингу состояния парка тепловозов и ключевых показателей эффективности транспортного хозяйства предприятия. Он позволит отслеживать работу в режиме реального времени, контролировать важнейшие показатели и оказывать поддержку в принятии решений на разном уровне управления.
— Расскажите об опыте цифровизации собственного бизнеса. Насколько он помог в период пандемии?
— Опыт наших предприятий — основа для предложения зрелых инструментов и услуг заказчикам. Заводы Siemens по производству продуктов для автоматизации (Factory Automation, FA) признаны мировым сообществом маяками цифрового производства. За счет внедрения новых цифровых технологий и принципов гибкого, бережливого производства на фабрике EWA в Амберге (Германия) с 1990 года в 14 раз вырос объем выпускаемой продукции без увеличения числа сотрудников и производственных площадей. Производство Siemens FA выполняет новый уникальный заказ за 24 часа, может перенастраивать производственные линии до 350 раз в день и выпускает 1200 вариантов высококачественных изделий.
Еще одна актуальная тема — устойчивое развитие. Так, «Сименс» поставил себе цель сократить CO2 до нуля к 2030 году. У нас сформировано «зеленое» портфолио — зарядные станции для электромобилей, оборудование для «зеленой» энергетики, солнечные электростанции — и есть энергоэффективные решения: «умные» сети, «умные» здания, цифровые двойники для энергосистем, цифровые подстанции, которые способствуют повышению надежности работы электросетевой инфраструктуры и сокращению затрат.
Пандемия COVID-19 повлияла на организацию бизнес-процессов, но нам удалось их перестроить относительно легко, так как их цифровизация запущена в компании достаточно давно.
Мы перешли на удаленные форматы работы с клиентами и после завершения пандемии продолжим развивать некоторые решения, которые выработали сейчас, — например, приложения и интернет-сервисы для удаленного мониторинга оборудования, удаленной приемки оборудования (вместо присутствия инженеров на местах), цифровые сервисы продаж и инжиниринговые платформы.