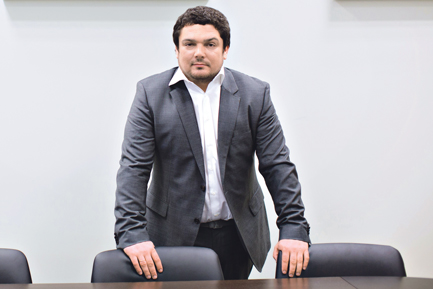
— Какие шаги в процессе импортозамещения вы, как глава одной из крупнейших инжиниринговых компаний России, назвали бы самими значимыми?
— Важно правильно определить, что мы подразумеваем под понятием «производство». Переклеить шильдик — это одно, собрать «железку» из зарубежных компонентов — это другое, а произвести самостоятельно все компоненты — это третье. Первый вариант отметаем сразу — считаю, что он не имеет никакого отношения к производству.
Сегодня темпы развития импортозамещения на бумаге опережают фактические возможности отечественных производителей по выпуску конкурентной продукции.
Одним из самых значимых шагов в этой области является проведение на уровне государства комплекса мероприятий по стимулированию создания высокотехнологичных производств. Это формирование территорий опережающего социально-экономического развития (ТОСЭР) с льготным налогообложением, упрощение процедур получения разрешения на строительство, специальные условия по прохождению таможенных процедур.
— Воспользовалась ли ваша компания какими-либо из этих льгот?
— Мы планируем в этом году открыть производственный центр на Дальнем Востоке в одной из ТОСЭР. Часть видов продукции будем производить сами, часть — в партнерстве с крупными иностранными компаниями. Сейчас ведем предметные переговоры, но пока я не могу раскрыть детали.
— Ваша компания реализовала крупные проекты по созданию центров обработки данных (ЦОД) для таких компаний, как «Газпром нефть», Сбербанк и другие. Было ли задействовано оборудование отечественного производства?
— Применение отечественных компонентов пока было возможно исключительно в использовании материалов, таких как силовой кабель, трубы и другие. Основное инженерное оборудование даже сегодня — импортное. Заказчики, не связанные жесткими обязательствами по импортозамещению, иных вариантов даже не рассматривают. Альтернатива производимому много лет высокотехнологичному иностранному оборудованию по мановению волшебной палочки не появится. Должно пройти время, прежде чем отечественные производители станут заметными игроками в этом сегменте.
— Ваша компания работала и работает на таких крупных объектах, как космодром Восточный, Серовская ГРЭС и другие. Какие сложности возникали при работе на этих предприятиях?
— Основные сложности работы на Восточном — удаленность объекта, сроки, нерегулярное финансирование, большое количество смежных систем и технологий. Считаю, что мы со своими задачами справились. Наши системы установлены, запущены и функционируют в штатном режиме.
Вопрос импортозамещения на этом проекте стоял очень остро, все бюджеты были утверждены еще при старом курсе рубля. Мы заменили вентиляционное оборудование, полностью перепроектировали холодильный центр, все, что можно, сделали в России. Получился эффективный симбиоз иностранной и отечественной продукции.
Сегодня работаем на Якутской ГРЭС, скоро выходим на Сахалинскую ГРЭС. На обоих объектах заказчик стремится использовать отечественное оборудование, но только тогда, когда оно действительно сравнимо с импортными аналогами или превосходит их.
— Каков ваш прогноз по переходу российских сервисных компаний на отечественное оборудование?
— Многие уважаемые западные производители на самом деле являются сборщиками. Например, ни один из ведущих производителей прецизионных кондиционеров не делает компрессоры и контроллеры, эти компоненты производит считаное число узкоспециализированных предприятий. Поэтому я считаю, что правильно для начала локализовать сборку. Тем более что многие иностранные производители, давно работающие на нашем рынке, наращивают здесь производственные мощности.
Что же касается менее сложного оборудования, то здесь возможны и варианты самостоятельного производства.